I have just finished watching a 3-part BBC documentary on "The Five Billion Pound Super Sewer", which follows workers across London as they race to build an enormous super sewer deep below the Thames. The existing system of tunnels and pipes was constructed in the Victorian era by an ingenious engineer Joseph Bazalgette. This amazing system functioned well for many years, but with London's booming population four times that of Bazalgette's time, the capital's sewage now overflows in heavy rain and the excess waste is diverted to take it out to the sea via the river. From 2023 this excess will be channelled down a 25 km long, 7.2 m wide Thames Tideway Tunnel, preventing millions of tonnes of untreated sewage flowing into the Thames each year.
The ingenuity of modern engineers has to be admired, but no more so than that of the Victorian engineers, who did not have the benefits of tunnelling machines, laser surveying etc. Bazalgette's brick-lined tunnels are a testimony to the skills of the 19th century engineers, but going back even further, there is a remarkable long forgotten system of tunnels in Cornwall, which were built in the 18th century, and hewn from the hard rock using hand tools and gunpowder blasting, long before the introduction of rock-drilling machinery. In 1843 the Mining Journal described the system as “the most extensive, valuable, and systematic undertaking of the kind in Cornwall, perhaps in England, and we believe but few in the world exceed it in importance”.
The Great County Adit is an extensive system of underground near-horizontal tunnels built to drain copper and tin mines in the Gwennap Parish, between Redruth and Bissoe in west Cornwall, once regarded as being "the richest square mile on earth". Construction started in 1748 and it eventually reached a length of nearly 40 miles (65 km) of underground tunnels, providing drainage to over 60 mines at an average depth of 80-100m.
Water has always been the enemy of the Cornish miner, and drainage has been crucial to the survival of Cornwall’s tin and copper mines. As shafts got deeper, adits (near horizontal shafts) were driven from around 1700 onwards to help drainage.
 |
Drainage adit: on the right a disused adit, still draining water from a long abandoned mine onto Perranporth beach, Cornwall |
However, even after the introduction of the steam engine, major problems remained for the ever deeper mines sited well inland in the St. Day and Gwennap areas. The water drained needed to be directed to the sea. The
Great County Adit, often known just as the
County Adit, provided the solution. The brainchild of
John Williams, owner of Poldice Mine, he and "adventurer"
Sir William Lemon drove the project forward. Begun in 1748, by 1760 it was draining Poldice Mine into the Carnon River which flows into Restronguet Creek, one of the River Fal's many creeks. By 1778 it had been extended to nearby Wheal Busy and
Wheal Peevor. Eventually it drained more than 60 mines in the Redruth and St. Day mining areas discharging around 13 million gallons a day into the river via its portal below the hamlet of Twelveheads. In the 1860s over thirty Cornish beam engines pumped into the adit, more than were used by the whole of continental Europe and America combined.
The high volume of water flowing out of the adit contributed to the success of at least 15 industries downstream from the portal at Twelveheads. There were tin dressing plants, two major arsenic producers, two blacksmiths, a small iron foundry, a corn mill and an ochre plant, the latter making use of the hematite flowing down from the adit. This vast amount of water, from the joining of several rivers and the County Adit, powered water wheels and was used in washing, but ironically the adit was the instrument of the decline of Devoran, the port on the Restronguet Creek which served the mines upstream via the Redruth and Chacewater railway. Disastrous floods in 1876 caused the neglected County Adit to release thousands of tons of water, carrying rubbish and silt down-river to Devoran, blocking navigation to all but the lower quays.
Although the mines have long been abandoned, and the adit is no longer maintained, it still drains the old workings, and in the summer of 1980 the flow was estimated at around 500,000 gallons per day, the river downstream still showing evidence of contamination by heavy metals.
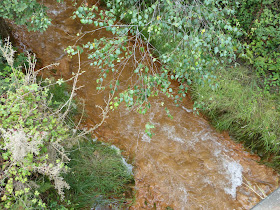 |
The Carnon River, near Bissoe, August 2018 |
 |
The County Adit portal in 1978
Photo: Roy Morton |
It is impossible to estimate the cost of driving the County Adit, but it is likely to have been around £250,000, a considerable sum at the time. However, this amount is relatively tiny considering the millions of pounds saved by the mines due to its efficient draining and the reduced cost of pumping to adit rather than to surface.
The Great County Adit is a reminder of a glorious past where Cornwall dominated world metal mining, and its story has been told in detail by
Alan Buckley, an ex-miner with extensive experience at South Crofty and Geevor mines. His book,
The Great County Adit, is published by the
Trevithick Society, and the photo on the front cover shows the adit portal at Twelveheads in 1978.